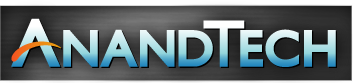
Original Link: https://www.anandtech.com/show/8201/the-asus-hq-tour-testing-facilities-qvl
The ASUS HQ Tour: Testing Facilities
by Ian Cutress on June 25, 2014 10:00 AM EST- Posted in
- Motherboards
- Asus
- Testing
- Testing Procedures
- Computex 2014
- QVL
- HQ
- Tour
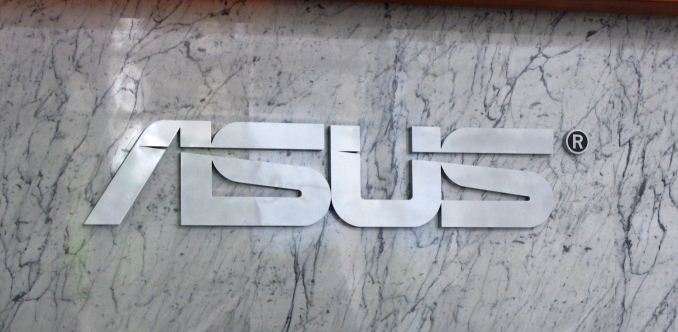
As part of our Computex trip this year, ASUS gave us a guided tour of its testing facilities at the ASUS headquarters in Northern Taipei. As part of this tour, we also spoke to engineers making sure that the features work to specifications, how they test, and also an interview with Dr Albert Chang, the Senior Division Director in R&D for the entire Motherboard Business Unit which will be in another post later this week.
It seems to be a common theme with motherboard manufacturer HQs in Taiwan: they all seem to be on the outskirts of the city limits. We have covered ASRock, ECS and GIGABYTE in the past, and with the exception of ASRock, the other two and ASUS have very obvious and dedicated buildings featuring the logo, as well as a dedicated entrance hall for visitors, employees, customers and the press. Even during our Friday afternoon tour, the building was very busy.
As with most of these companies, the entrance to the building is adorned with artworks and company philosophies. To the right of the front door is a Mona Lisa crossed with a surreal melting Dali-esque frame, with the image made from motherboard PCB components:
Whereas right ahead is a cast bull, also adorned in PCB components:
On each side of the entrance is the ASUS Business Philosophy – one side to the left in Chinese:
And handy for us foreigners, the English version opposite:
ASUS, like many other large technology companies, offer facilities to their employees in terms of food and fitness. The HQ offers a gym, a swimming pool and a full sized sports hall:
At the end of my tour, back at the second floor coffee shop, this hall had become full of people playing volleyball in different guises. As many Asian businesses like to do, keeping their employees fit and healthy (and perhaps monitoring their physical fitness) is part of promoting a strong work ethic.
Despite being a building that only employees (and guests) can enter, it seems to make business sense to open a Starbucks franchise just below the gym and pool. As a side-business in the building to keep the workforce happy, I assume ASUS does not need to make profit on this, and it is worth noting that my tour guides each had 200 NT (Taiwanese Dollars, about $6.60) to spend in the nourishment facilities in the building per day.
For those employees that worked later hours, beyond 6PM even on a Friday, the food hall provided six different types of food including vegetarian, native Taiwanese cuisine, Korean cuisine and a buffet style service.
Next to the cash machine and banking facilities was this little gem – one of ASUS’ posters to help reduce waste within the company and aim to keep energy use down.
My tour consisted of two main parts – a trip upstairs to a testing and QVL lab, and a trip to the basement for the extended testing facilities.
The ASUS HQ Tour: QVL
When you purchase a motherboard, a quick look on the website reveals the Qualified Vendor List. This list shows all the additional components that have been certified to work in the motherboard, and a typical list includes processors and memory, with the required BIOS version in order to make that component work properly. At the end of the day, it is someone’s job to test all that hardware – imagine testing a large chunk of the memory modules and capacities available, and then multiply that testing with each motherboard that comes to market. Clearly one person and one test bench is not going to get through each motherboard in time for launch, especially if compatibility testing is more than just ‘plug-it-in’ and ‘see-if-it-works’. ASUS uses a series of stress tests to ensure that every component on the QVL test is examined in detail for compatibility. As a result, insert rows upon rows of testing equipment:
In the weeks leading up to release, each one of these racks will hold 3-4 systems per shelf with what looks like a KVM switch for control management.
On the right here are several racks of DRAM, ranging from the regular DDR3-1333 2GB modules that were first launched with DDR3 all the way up to Apacer DDR3-3200 kits, as well as the 8x8 GB memory kits. It is worth noting that when a memory kit appears on the QVL, it means that the kit used on its own is the only thing tested – not when multiple kits (even those of the same type) are put together. ASUS ROG Admins often suggest against using two kits of the same memory in the same system, as there is no guarantee they will work together.
Over the past twelve months, most motherboard manufacturers have discussed audio testing especially in relation to the extra engineering this area of the motherboard receives. With some of the new audio features on the Maximus VII ROG motherboards for Z97, ASUS took me through their verification process. For line-out, an analog audio signal is generated and sent to their $50k Audio Precision hardware:
This processes the signal, compares the data to the original file, and sends the results back to the system for further analysis. With this hardware they can simulate various impedance levels of headphones to ensure that the frequency response is as accurate as possible. The reverse happens as well, testing the line-in using a digital output through the motherboard and a DAC to ensure the motherboard input is the limiting factor.
ASUS discussed some of their audio features are a bit of give-and-take, for example the frequency response at around 50 Hz with the regular codec actually drops around 5 dB. In order to get a better frequency response at this end of the hearing range, a buffer is implemented to make the response more accurate, which has some effects on disortion and THD+N. In order to help minimise this side-effect, some motherboards (such as the M6F) uses a pair of DACs that have a lower THD+N than the codec. This all comes at a small expense for onboard audio due to using extra components, but this is where the extra engineering for a motherboard comes into play for product comparisons.
The ASUS HQ Tour: Endurance Testing
All consumer electronics, in order to be deemed safe for use, have to go through a certification process based on electrical noise, impact testing, vibration testing and heat testing. This is becoming especially more important in the motherboard space as these certifications can act as selling points, or help ensure a lower return rate. Typically these testing areas at motherboard manufacturer headquarters are off-limits to almost everyone, but we had special permission and a tour guide to take us through. These are also often secret areas, and we were unable to take pictures, however ASUS appointed one of their PR team as a photographer and provided vetted images after this part of the tour. These images are what I saw with my own eyes, and there are no obvious parts that ASUS left out from these images from what I was shown.
The bit of the tour I was most excited to see was the semi-anechoic chamber. These rooms are awesome (this was my second visit to one), because they are usually several stories underground and designed to minimise any form of noise whatsoever.
The walls and ceiling are made with noise dampening materials, and we were far enough underground to avoid any large trucks producing additional noise. The purpose of this room is to detect electrical interference on a product, or to test audio hardware. Standing in this room without making a noise in certainly eerie, because the loudest thing you can hear is the blood rushing through your ears. There are scare stories about how one of these rooms can drive you insane, because even talking in an anechoic chamber is strange given that the sound does not bounce off the walls. All you can hear is the sound that comes directly at you, there is no echo. When we moved outside of the room back into the control room, the screens showed that the base level of noise was at 15 decibels. To put that into perspective, 30 dB is the sound of a leaf rustling, and due to the logarithmic scale of sound, that 15 dB difference equates to a 32x quieter sound than a leaf. So what is making 15 dB of noise when the room is closed? It comes from the electrics, such as the hum of capacitors or the light bulbs. If anyone has a chance to experience such a room, I highly recommend it.
In one of the testing rooms is this machine, an impact tester. The motherboard is fixed to the red block in the middle, and raised several feet in the air:
The whole apparatus is then dropped (under gravity) and then checked for loose components. This process is repeated as required.
This is a big vibration machine, shaking the system either horizontal axis several dozen times a second. Again, this is another test to verify that the system does not fall to bits and still works after quick changes in impulse forces.
Ever wondered how manufacturers can offer a MTBF (mean time between failures) value even when they cannot have tested for that long? Well at this point we have the heat chamber, and as this sign suggests, forty systems are subjected to a 40ºC ambient temperature at a high humidity for sixteen days while running benchmarks such as 3DMark.
As is typical for an event like Computex, I was in a suit, and I walked into this room. It was certainly hot, especially with the circulating air and the high humidity. Within about 20 seconds my brow was starting to sweat, and after 60 seconds I left the room with sweat forming behind my ears. In the past we have seen motherboards that have been certified to run in these environments or warmer, for longer, as a selling point for the product. More often than not, this sort of testing is also a major part of a server product, but ASUS’ TUF line is also subject to this stress.
Another element of the TUF Range, along with the longer warranty, is meant to be its ability to withstand stress. I saw one room in the testing facility where motherboards were wired up to pressure sensors in the key areas:
This motherboard was then subject to localized pressure point testing:
Here this device is forced onto the motherboard, simulating pressure up to a specified range. The device moves about the motherboard, including all the spots typically weak, to find if the motherboard with the TUF Fortifier breaks or if it becomes unusable.
There was also a twist test:
Here the system is placed under torque, or more precisely, a rate of change of torque per unit distance. This makes the motherboard twist repeatedly (the machine reversed direction every couple of seconds), such that there was a definite bend to it:
This amount of bend might seem unreasonable for a normal usage scenario, especially for the end-user, but there are obvious advantages to testing the motherboards almost to destruction at this point.
I asked about how many motherboards go through this procedure. It was obvious that not every motherboard does, otherwise not many would go on sale. The answer was less clear, though every batch has a proportion of motherboards taken and tested. If those pass the tests, then the batch is clear for sale.
Many thanks to ASUS for the tour of its testing facilities, and for seeing how the staff in the main HQ are catered for. Below is a full gallery of the images we took for the visit, and look out for the transcript from our interview with Dr. Albert Chang, Senior Division Director in R&D for the entire Motherboard Business Unit, in the next few days.